Record players and turntables are outstanding feats of engineering. I hear all the time from new vinyl collectors about how amazing they find the playback process of a vinyl record.
It’s little wonder folks find the mechanics of how a record player works so fascinating. After all, it’s a miracle the process even works at all!
In the following guide, we’ll explain the parts of a record player so you can better understand how a turntable actually makes sound.
Next time somebody says, “how does that even work”?! You’ll be able to impress them with your analog wizardry; it’s quite ironic that despite so much progress in technology, many are more impressed by older tech like the physical playback of music than its digital counterpart.
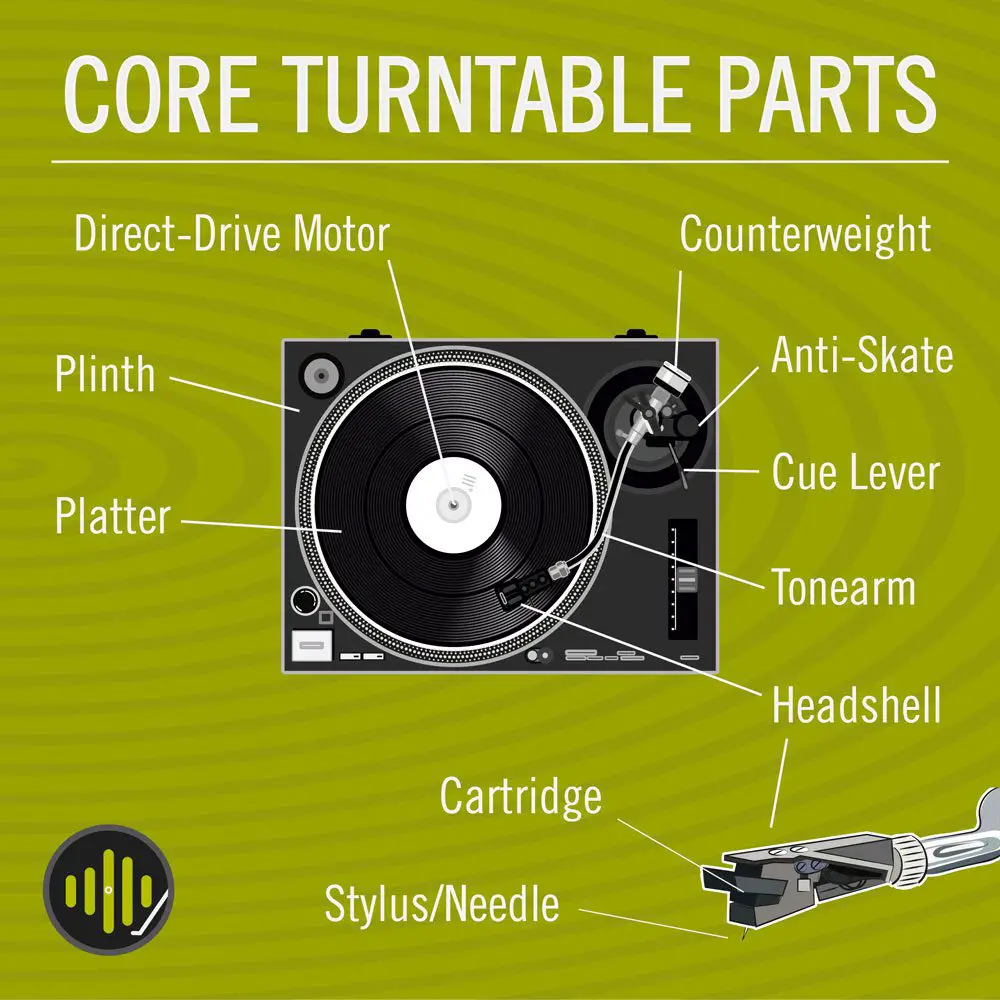
Mechanical Roots
In our digital age, we take for granted that recording and playing back of music was once an entirely mechanical process. Yep, you read that right: no electricity required – just pure mechanics.
The first working record player goes back to 1877, when Thomas Edison unveiled the phonograph.
It was the first working machine that could record and replay sound. The device consisted of a cylinder wrapped in tin foil that a hand crank could turn.
When sound entered the mouthpiece, a diaphragm and attached needle would vibrate, making indentations in the foil. Reverse the process, and there you have it, a replayable recording.
Later down the line, German-American inventor Emile Berliner would introduce the concept of a flat rotating platter and disk, which paved the way for the modern turntable.
Record players and turntables have come on a long way since our ancestors first experimented with etching vibrations into foil-coated cylinders, but in many ways, our modern record players are still based on some of their founding principles. If you’d like to learn more, check out our full history of record players and turntables.
The Parts of a Record Player Explained
It helps to have a basic understanding of the core parts of a record player, the purpose of each component, and what makes them perform at their best.
Below are the fundamentals that every vinyl fan should know:
Isolation Feet
To build a solid house, so to speak, we must start with solid foundations. Isolation feet are the pillars of any turntable and a much-overlooked component in providing a stable platform and controlling unwanted resonance.
The better we can isolate our turntable or record player from outside vibrations (both in the air or from vibrating surfaces), the better it will perform. External vibrations can make their way to the stylus through the turntable components, thus making their way into our HiFi system. The less this happens, the better.
Good quality isolation feet will help control unwanted resonance, either through damping material (such as TPE rubber) or spring components. An alternative approach is to minimize contact with the surface by using spikes. Similarly to how speaker feet work, the less contact we make with the surface, the less room for pesky vibration to transfer from one object to another.
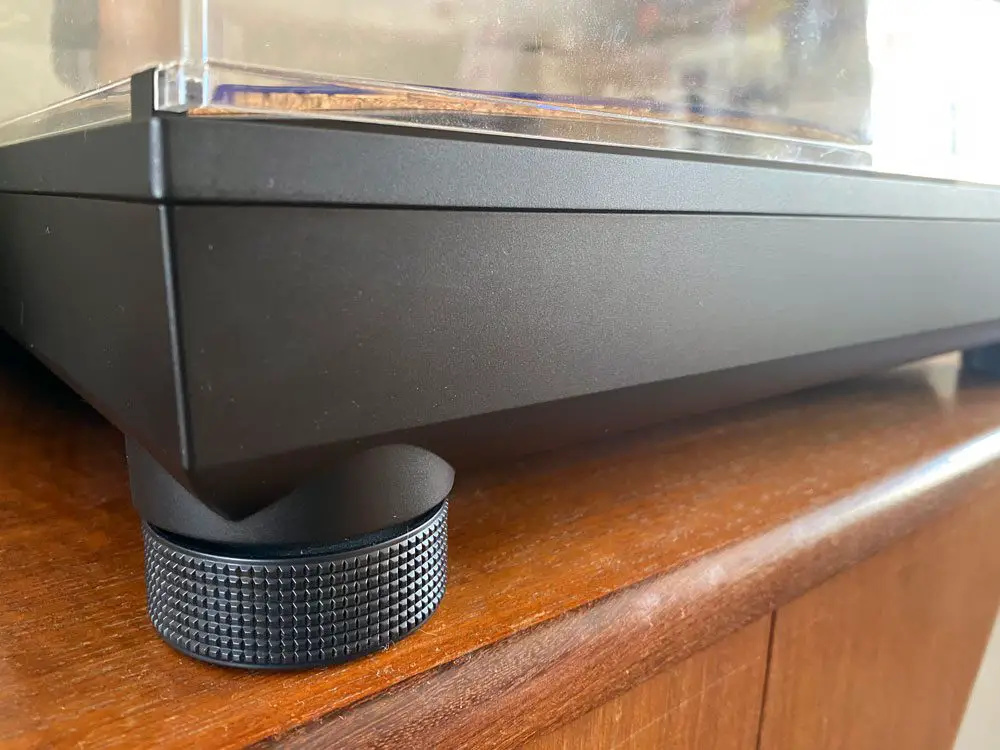
The Plinth
Moving up in the world, we have the plinth. Supported by the isolation feet, of course, the plinth is our main base upon which everything else sits – or the other vital components reside.
A good quality, solid plinth will aid further in controlling resonance. Depending on the type of record player, different materials are used to construct the base, from MDF to many varieties of wood – even metal and plastic.
Solid bases are thought to control resonance very well, but there are examples of hollow units (particularly with DJ decks from the likes of Technics) where the chassis has to be hollow to house the circuit board components. In this case, there are other approaches to controlling resonance. For example, my Technics SL1500 is made from a dual-layer construction of die-cast aluminum and ABS (essentially a posh durable plastic) mixed with fibreglass.
Another approach to plinth design is to keep the surface area as small as possible, thus by design keeping the potential for excessive resonance as low as possible.
The Platter (or Turntable)
The terms record player and turntable are often used interchangeably. But when you understand the history of record players and the evolution from wax cylinder designs to flat records on a rotating platter (otherwise referred to as a turntable), you can see where the terms originated.
If you want to draw a line between the two, most record collectors define all-in-one units with built-in speakers as “record players”, and separate decks that require an external amp and speakers as “turntables”.
Originally, however, the turntable was simply the rotating surface on which your records sit.
Platter materials vary greatly, but the best designs have high mass for better speed consistency and dense construction to control resonance.
Metal platters tend to suffer from resonance, and very light aluminum designs don’t provide the ideal mass. Acrylic and glass plinths are popular for mass and resonance controlling properties. Both sound different, but acrylic is basically acoustically dead; glass has a certain sound quality that some listeners enjoy.
All designs, of course, have a metal center spindle that holds the record in place while the platter spins.
The Drive System
A drive system (housed by the plinth) is the motor that drives your platter. There are two different drive system designs, both of which have their merits:
Direct Drive: With a direct-drive turntable, the platter sits directly on the motor. This motor “directly” drives the turntable.
Belt Drive: In the case of a belt-driven turntable, the motor sits off to the side of the platter. In other words, they are decoupled. A rubber belt loops around the motor and also the platter. When the motor spins, the belt drives the turntable.
For more on this topic, read our direct-drive vs belt-drive article.
Belt-driven turntables are favored by the audiophile community. The reason being, decoupling the motor reduces resonances, which can make its way from the motor to the platter, and ultimately, into the audio system through the stylus.
Direct drives have higher torque, meaning they get up to speed quicker and stop much faster. This traditionally makes them preferable for DJ applications.
There’s also the question of speed consistency, which can be better on a good direct drive system when compared with the issues of worn belts on a belt-driven deck.
The Tonearm
A tonearm tube pivots from the edge of the record towards to center. At the end of a tonearm is your cartridge, which has a needle (better known as the stylus) responsible for tracking your record’s groove.
The part that holds your cartridge is called the headshell – some manufacturers use detachable headshells to make swapping cartridges easier, while others prefer the rigidity that comes with a single piece of tubing with no break.
At the other end is your counterweight, which needs to be set correctly to apply the proper amount of tracking force.
Most tonearms pivot from a full bearing, but there is a growing trend toward using uni-pivot designs that seek to keep bearing friction to a minimum by reducing the contact area of the moving surfaces.
The name of the game here is absolute rigidity but nimble performance; the tonearm must be extremely stiff and strong, while also very light in weight. There can be no flex or movement in the tube while the cartridge is on the record, and the bearing from which the tonearm pivots should not allow the tonearm to wobble in any way.
Materials such as aluminum & carbon fiber became popular for their strength and rigidity while remaining light and nimble. It stands to good reason that a lighter tonearm with less inertia will respond better to groove modulations and slight changes in the record surface, and therefore track the record more accurately.
Most tonearms are either straight or s-shaped. Like most things in audio, there are pros and cons to both:
It all comes down to a balance between mass and the benefit of having equal mass distributed on either side of the tonearm’s pivot. S-shaped tonearms have the upper hand here, but as a trade-off, they can have greater mass as the arm is longer overall. Also, a longer tonearm allows for less tracking error as the tonearm moves across the record in an arc.
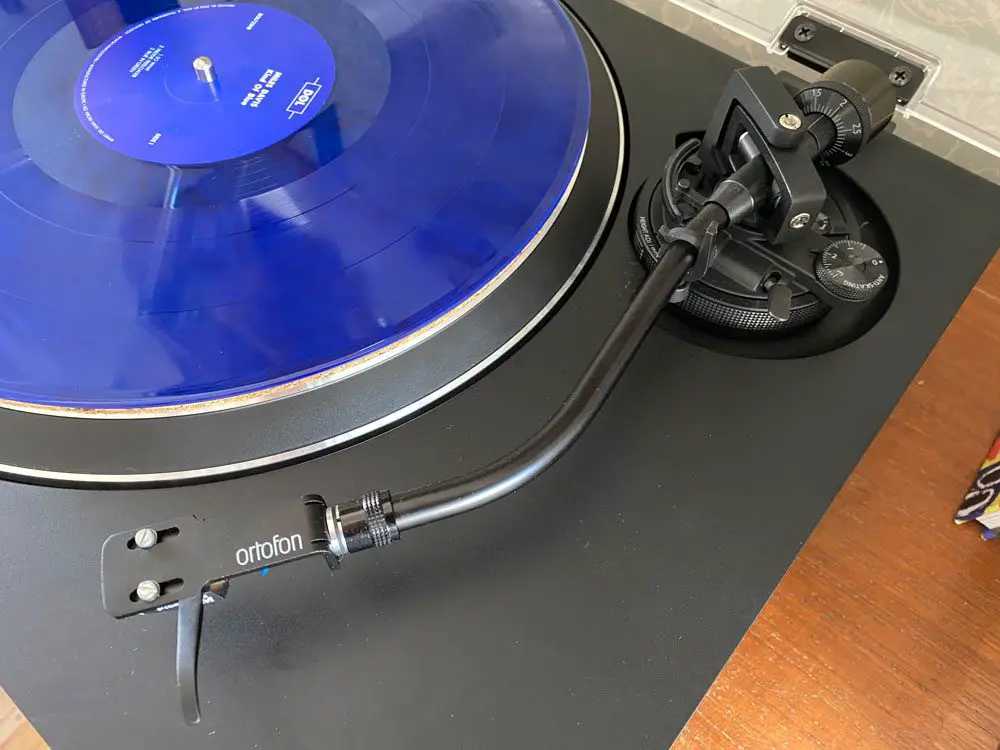
Tonearm Anti Skate
Anti skate mechanisms take several forms, from easy to adjust dials to very simple weights attached to the tonearm.
Either way, the job of anti-skate on a turntable is to offset the inward-directed momentum of the tonearm. Without anti-skate, this bias towards the center will cause the stylus to ride one side of the groove, causing tracking errors, poor sound quality, and ultimately, increased record wear.
Cartridge and Stylus
Put very simply, your cartridge and stylus track the record groove, turning the vibration into an electrical signal we can amplify in the audio system.
The stylus (some call it a needle) is a small metal cantilever with a diamond tip. As the cantilever vibrates according to the groove shape, magnets and coils generate a tiny, passive audio signal that travels up the cables inside the tonearm tube.
That’s a pretty crude explanation, but it’s enough for the purpose of this article.
There are two types of cartridge design: moving magnet (MM) and moving coil (MC). As you might be able to guess, with MM designs, it’s the magnets that vibrate, whereas MC designs generate the signal as the coils move within a magnetic field.
MM cartridges are much cheaper to produce and allow the user to replace their own stylus. MC cartridges have superior detail and frequency response, but can be expensive and don’t typically allow for user-replaceable styli.
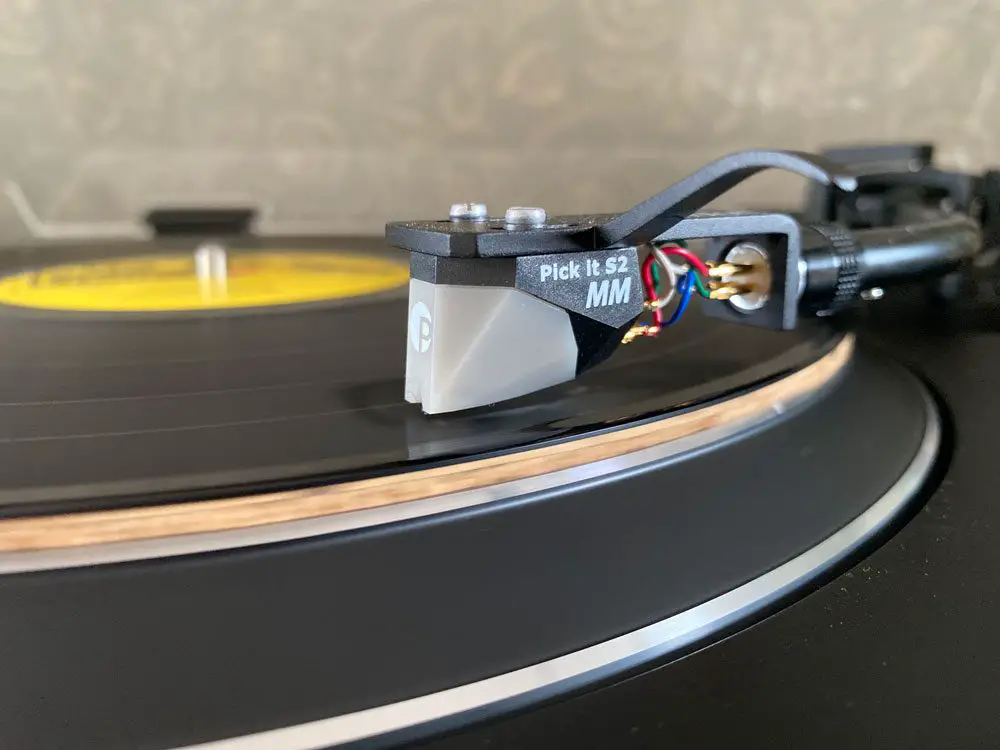
The Bottom Line
Naturally, from one turntable to another, there are always different approaches, features, and materials. However, the core parts of a record are fundamentally based on the same basic principles going back over 100 years.
Vinyl records might be older technology by today’s digital standards, but old certainly doesn’t mean obsolete. Given the continued resurgence and popularity of vinyl records among a broad age range, it’s easy to see how this timeless medium stands the test of time.
Ever evolving, engineers continue to improve on timeless principles and solid foundations. The story of vinyl records and turntables isn’t over just yet.
What a comprehensive guide to the anatomy of a vinyl record player! This article from Your Sound Matters brilliantly demystifies the intricate components, making it accessible for both beginners and seasoned vinyl enthusiasts. The detailed breakdown of each part, coupled with clear explanations, is invaluable for anyone looking to understand and appreciate the inner workings of their turntable. Kudos to Your Sound Matters for shedding light on the essential elements that bring our vinyl experience to life.
What does the spindle rotate on? What kind of “ball bearing” is in the bottom of the shaft?